Know the Difference: ABS vs. PVC 3mm Edgebanding
When it comes to edgebanding, the choice of material is crucial. Of the many options available, ABS (Acrylonitrile Butadiene Styrene) and PVC (Polyvinyl Chloride) stand out as the most popular choices. Each material has its own advantages and disadvantages and is suitable for different applications. In this article, we will explore the differences between the two materials, focusing on their characteristics, installation process, and environmental impact.
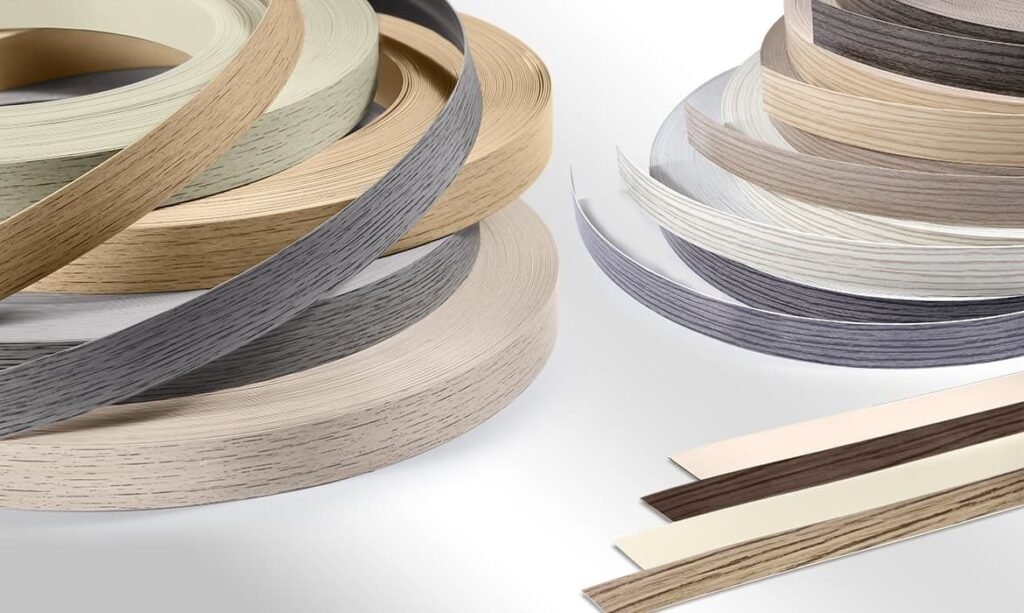
Know the Basics: ABS vs. PVC
Both ABS and PVC are widely used in edgebanding, providing a durable surface to protect the edges of the board.
ABS is a plastic polymer known for its ease of use and environmentally friendly properties. While it is generally more expensive than PVC, it is fully recyclable and biodegradable. ABS shrinks at temperatures as high as 99 degrees Celsius, making it more stable at high temperatures.
PVC, on the other hand, is an affordable option that is often used for edgebanding. It shrinks at lower temperatures of 70 degrees Celsius, which can cause problems in certain applications. While PVC is durable, it is less environmentally friendly and less fire-resistant than ABS.
Environmental Impact
ABS has the upper hand when it comes to environmental footprint. Both materials can be recycled, but ABS is considered the more environmentally friendly choice. It breaks down faster in landfills and does not release harmful gases when recycled through burning. In contrast, while PVC is recyclable, it takes longer to break down and releases toxic gases when burned.
Fire Resistance
Both ABS and PVC are fire resistant, but they differ greatly in this regard:
PVC is fire resistant, but in the event of a fire, it releases harmful gases that pose a health risk.
ABS is generally more fire resistant, and even if it does catch fire, the chance of exposure to toxic gases is greatly reduced, making it a safer choice for a variety of applications.
Durability
Durability is a key factor when choosing an edgebanding material.
PVC is more resistant to solvents and UV rays, and it can withstand even the most powerful cleaners without damage.
ABS is slightly less resistant to UV rays and strong solvents, but it is manufactured with high-quality pigments designed to prevent discoloration and fading over time.
Cost Factors
From a cost perspective, PVC is a more affordable option, making it an attractive choice for budget-conscious projects. ABS tends to be more expensive than PVC and other plastic materials. However, this higher cost also comes with some benefits, such as easier processing and being more environmentally friendly.
Processing and Installation
When it comes to processing and installation, ABS is often the material of choice. It is easier to work with on edge banding machines, and trimming knives used for ABS last longer. In contrast, PVC is more challenging to process due to its sturdy composition, although it can withstand strong solvents, making post-application cleanup easier.
Another notable difference in the installation procedure is the use of laser technology. ABS is fire-resistant and does not produce toxic fumes when burned, making it compatible with laser technology. However, PVC should not be used with laser or Air-tech technology because it releases harmful gases during the burning process.
Tinting Strength and Size Variety
Both ABS and PVC have excellent tinting strength and use similar printing technologies. However, PVC manufacturers generally offer a wider range of widths and thicknesses, providing greater size diversity. If your project requires a specific size that ABS cannot accommodate, PVC may be a better choice.
Final Verdict
So, which material is better: ABS or PVC? The answer depends on your specific needs and restrictions. If you need laser applications, ABS is your only choice. If you are looking for a more affordable solution or need a specific size, PVC may be your best choice.
Before making a decision, it is important to weigh all factors – environmental impact, fire resistance, durability, cost, processing and installation.
3mm Edgebanding Conclusion
Choosing between ABS and PVC edge banding requires careful consideration of various factors. Both materials have their own advantages and disadvantages, and the best choice depends on the specific requirements of the project. Whether you choose more expensive, environmentally friendly and fireproof ABS, or affordable, durable and solvent-resistant PVC, you can rest assured that you have chosen a material that will provide a solid surface to protect the edges of the board.
For inquiries about 3mm edge banding solutions, please contact Shanghai Luyao Industrial Co., Ltd.:
Leave a Reply