How Precision edge banding for kitchen cabinets durability & design
Forget the flashy hardware or the exotic wood veneers for a moment. The true mark of a premium kitchen cabinet – the element that separates fleeting trends from lasting value – lies hidden in plain sight: the edge banding for kitchen cabinets. As a leading manufacturer immersed in the science and artistry of edge protection, we understand that this seemingly humble strip is the unsung hero, the critical barrier between pristine beauty and premature deterioration. It’s not just a finishing touch; it’s the foundation of cabinet longevity and aesthetic integrity.
Beyond the Veneer: The Harsh Reality of edge
Imagine your stunning new kitchen. Now, zoom in on the raw, exposed edge banding for kitchen cabinets, drawer box, or panel end. That’s the Achilles’ heel. Particleboard, MDF, and even plywood cores are inherently vulnerable. Without protection, they act like sponges, readily absorbing ambient moisture from steam, spills, and even humidity (studies by the Forest Products Laboratory show untreated MDF can swell by 15-20% within 24 hours of water exposure). This leads to unsightly swelling, warping, and delamination – the dreaded “chipboard bloom.” Friction from daily use chips and scuffs the fragile surface, while UV light fades exposed edges unevenly. The result? A cabinet that looks tired and damaged long before its time. A 2024 National Kitchen & Bath Association (NKBA) report indicated that 38% of premature cabinet replacements cited “edge failure or deterioration” as a primary factor – a costly and avoidable problem.
The Evolution of edge banding for kitchen cabinets: From Cover-Up to Core Component
Gone are the days when edge banding for kitchen cabinets was merely a cosmetic afterthought. Modern manufacturing demands, coupled with consumer expectations for durable, beautiful, and sustainable products, have propelled edge banding into a sophisticated engineered solution. We’re not just selling strips of material; we’re providing engineered armor, seamless aesthetics, and environmental responsibility.
Material Mastery: Choosing the Right Shield
The core material dictates the banding’s performance. Understanding the nuances is crucial:
- Advanced PVC (Polyvinyl Chloride): The Workhorse Reinvented: Still the dominant choice (holding approx. 65% of the global edge banding market according to Grand View Research 2025), modern PVC is leagues ahead. Forget brittle, limited options.
- High-Pressure Modified Resins: We utilize proprietary formulations incorporating impact modifiers and UV stabilizers. Lab tests show these formulations increase abrasion resistance by 40%+ compared to standard PVC and reduce color fade by 30% under accelerated UV testing (ASTM G154).
- Ultra-Realistic Decors: Digital printing and sophisticated embossing techniques (like 7D laser engraving) create wood grains indistinguishable from natural veneer, including intricate figured maples, rift-cut oaks, and even concrete or metallic finishes. Color matching technology ensures seamless integration with any laminate or painted finish.
- Functional Additives: Options now include:
- Antimicrobial Protection: Integrated silver-ion technology inhibits mold and bacterial growth (tested to JIS Z 2801/ASTM G21), crucial for hygienic kitchens.
- Enhanced Chemical Resistance: Formulations specifically resistant to common kitchen cleaners, oils, and acids.
- Soft-Touch Finishes: Luxurious matte textures providing tactile appeal and superior fingerprint resistance.
- Engineered Wood Veneer: Nature Enhanced: Real wood beauty demands real solutions. Our engineered veneer banding isn’t just sliced wood; it’s optimized performance.
- Cross-Grain Stabilization: Thin veneer layers are cross-laminated under high pressure. This counteracts wood’s natural movement, reducing susceptibility to seasonal cracking or lifting by over 50% compared to traditional single-ply veneer banding.
- Pre-Finished Durability: Factory-applied, catalyzed UV-cured finishes (polyurethane, acrylic) offer far superior scratch, stain, and moisture resistance (>300 MEK rubs, >4H pencil hardness) than post-application staining. A 2025 Woodworking Network survey found 72% of cabinetmakers prefer pre-finished veneer banding for consistency and time savings.
- Sustainable Sourcing: Utilizing rapidly renewable species (like Poplar, Acacia) and FSC-certified veneers ensures ethical and ecological responsibility. We track chain-of-custody rigorously.
- ABS (Acrylonitrile Butadiene Styrene): The Premium Alternative: Gaining significant traction (projected 12% CAGR 2024-2030), ABS offers distinct advantages:
- Superior Impact Resistance: Inherently tougher and more flexible than PVC, ABS is virtually unbreakable during handling and installation, and highly resistant to chipping in service. Drop tests show 2-3x higher impact resistance than standard PVC.
- Exceptional Thermal Stability: Withstands higher temperatures without warping or adhesive compromise, making it ideal near ovens and cooktops. Remains stable up to 185°F (85°C) continuously.
- Eco-Profile: Often contains recycled content and is fully recyclable (Recycling Code #7). Chlorine-free composition appeals to environmentally conscious specifiers.
- Brilliant Solid Colors & Gloss: Achieves deeper, more vibrant solid colors and higher-gloss finishes than PVC.
- PP (Polypropylene): The Flexible Contender: Best suited for curved applications or budget-conscious projects requiring good moisture resistance and flexibility. Less common for high-wear edge banding for kitchen cabinets but useful for specific profiles. Recycling Code
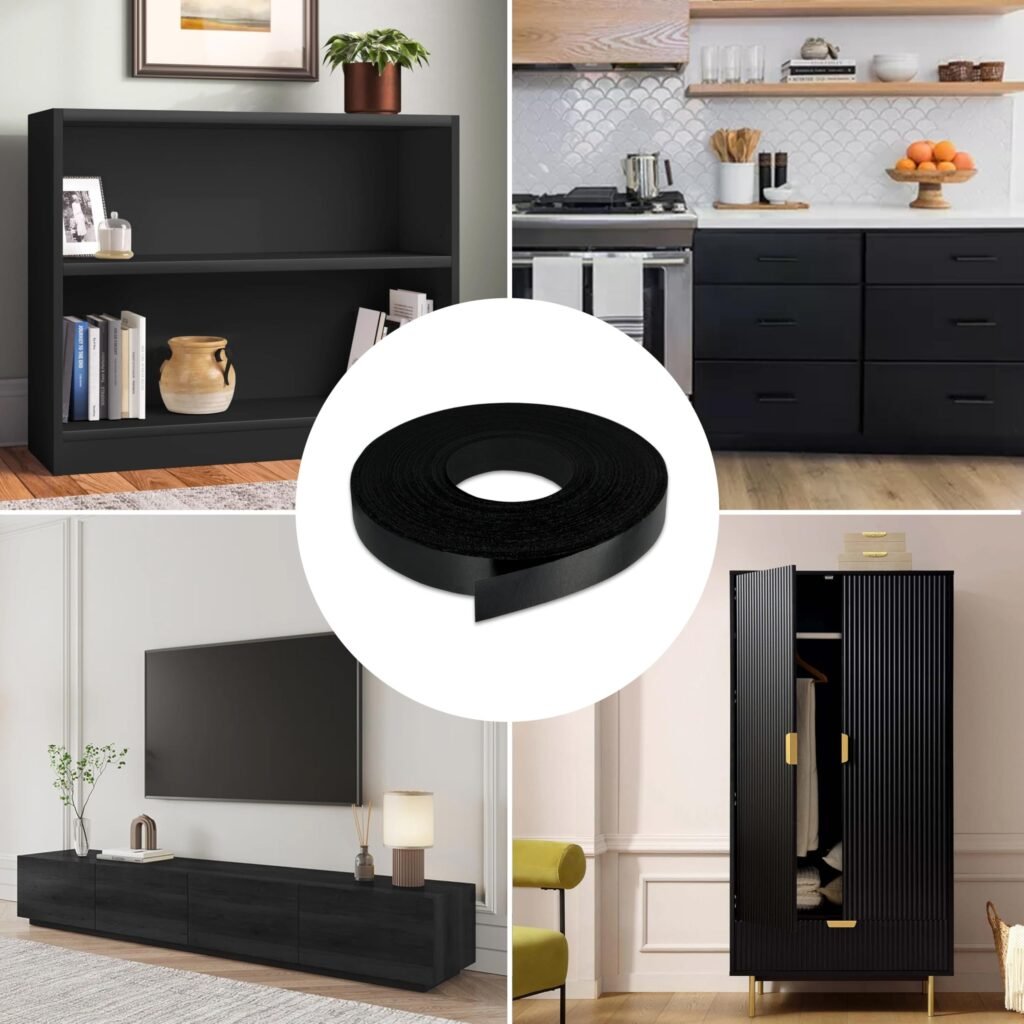
Thickness & Width: Precision Matters
Selecting the right dimensions isn’t arbitrary; it’s engineering:
- 0.4mm – 0.6mm: Primarily decorative, for very low-impact areas (e.g., cabinet backs, display unit tops). Not recommended for functional cabinet edges.
- 0.8mm – 1.0mm (The Kitchen Standard): Our most recommended thickness for all kitchen cabinet edge banding for kitchen cabinets (doors, drawer fronts, shelves, gables). Provides optimal balance of durability, seamless appearance, and cost-effectiveness. Offers significant protection against chipping and moisture ingress while maintaining a fine, furniture-like edge banding for kitchen cabinets. Industry data shows over 85% of quality kitchen cabinet production uses 0.8mm or 1.0mm banding.
- 2.0mm – 3.0mm: Heavy-duty applications. Used for commercial counters, high-impact areas (e.g., kick plates), or for creating a deliberate, bold edge profile (“square edge” look). Adds substantial impact resistance but requires specialized application equipment. Represents less than 10% of residential kitchen use.
Width is equally critical. Standard ranges (18mm, 22mm, 26mm, etc.) must precisely match panel thickness after any sanding. We offer custom width slitting (9mm – 100mm) with tolerances of +/- 0.1mm to ensure perfect coverage without costly over-trimming or unsightly gaps. A poorly matched width instantly signals low quality.
The Adhesive Revolution: The Glue That Holds It All Together
The decorative layer is only half the battle. The adhesive bond is the true determinant of longevity. The era of problematic hot melt is fading:
- The Problem with Traditional Hot Melt (EVA): Susceptible to heat reactivation (steam, oven proximity), has limited moisture resistance, and can become brittle over time, leading to the infamous peeling edges. NKBA estimates failures related to EVA adhesives cost the industry over $150 million annually in warranty claims.
- PUR (Polyurethane Reactive) Adhesive: The Modern Standard: This is where true performance begins.
- Chemical Bonding: PUR reacts with moisture (in the air and the substrate) to form an unbreakable, cross-linked molecular bond. It doesn’t just stick; it becomes part of the material.
- Unmatched Resistance: Impervious to heat (stable beyond 250°F/120°C), moisture, steam, and most chemicals. Lab immersion tests show zero delamination after 1000+ hours.
- Gap-Filling Properties: Compensates for minor substrate imperfections, ensuring a 100% contact bond line. This is critical for preventing moisture wicking.
- Long Open Time: Allows for precise positioning before the bond fully cures. We exclusively use premium, high-solids PUR adhesives on our performance banding lines.
- Laser & Hot Air Welding: The Seamless Future: The pinnacle of edge technology, using zero liquid adhesive.
- The Process: Precisely focused laser energy or superheated air melts the thermoplastic back of the edge banding (PVC, ABS, PP) and the very surface of the substrate (typically MDF/PB).
- Molecular Fusion: The molten materials intermingle and fuse upon cooling, creating a homogeneous, monolithic bond – essentially becoming one piece.
- Absolute Impermeability: Creates a 100% waterproof seal, making it ideal for wet environments like bathrooms and kitchens prone to spills. Independent testing (e.g., DIN EN 205) shows superior strength and moisture resistance compared to all adhesive methods.
- Invisible Seam: Achieves the closest possible “zero joint” appearance. Requires significant investment in machinery ($250k+), limiting it to high-end manufacturers, but representing the ultimate in quality and durability. Adoption is growing at 18% YoY among premium cabinetmakers.
Beyond Basics: The Cutting edge banding for kitchen cabinets
Innovation continues to redefine possibilities:
- Integrated Lighting Channels: Precisely extruded channels within clear or translucent ABS/PMMA banding allow for seamless integration of LED lighting, creating stunning under-cabinet or accent lighting without visible fixtures.
- Hybrid Materials: Combining layers (e.g., ABS top for durability with a recycled PP core) optimizes performance and sustainability.
- Digital Customization: On-demand printing allows for ultra-short runs of bespoke colors, patterns, or even branded edge banding for kitchen cabinets
- Enhanced Sustainability: Bio-based polymers (e.g., derived from castor oil), significantly increased recycled content (up to 90%+ in some PP formulations), and solvent-free manufacturing processes are key focuses. We track and minimize our carbon footprint per meter produced.
- “Smart” Banding: Early R&D explores integrating subtle sensors for moisture detection or temperature monitoring within the banding profile.
Why Partner with a Specialist Manufacturer?
Choosing your edge banding for kitchen cabinets supplier is as critical as choosing the cabinet manufacturer. Here’s what sets a true partner apart:
- Vertical Integration & Quality Control: Controlling the entire process – from polymer compounding/veneer selection through precision extrusion/coating, printing, and adhesive application – ensures unmatched consistency. Our in-house labs perform daily quality checks on thickness, color (spectrophotometer), adhesion (peel strength, boil tests), flexibility, and surface resistance.
- R&D Investment: Continuously developing new materials, adhesives, and finishes isn’t a luxury; it’s a necessity to solve real-world cabinet challenges. We allocate over 5% of revenue to R&D annually.
- Technical Expertise & Support: We don’t just sell product; we provide application guidelines, troubleshooting, and machine compatibility advice. We understand the pressures of your production floor.
- Reliable, Scalable Supply: Consistent quality and on-time delivery are non-negotiable. Our global manufacturing footprint ensures supply chain resilience. Capacity exceeds 8 million linear meters monthly.
- Commitment to Sustainability: Transparent reporting, certified sustainable materials (FSC, GREENGUARD Gold), energy-efficient production, and recyclable packaging are core principles. We aim for zero manufacturing waste to landfill by 2028.
The Bottom Line for Cabinet Makers & Designers
Specifying the right edge banding isn’t an upcharge; it’s an investment in reputation, reduced warranty costs, and customer satisfaction. A cabinet is only as good as its weakest edge. By demanding:
- Material Excellence: (Advanced PVC, Engineered Veneer, ABS)
- Precision Thickness: (1.0mm for most edge banding for kitchen cabinets)
- Uncompromising Adhesion: (PUR or Laser/Hot Air)
- Manufacturer Expertise
…you ensure the cabinets you create or specify deliver lasting beauty, unwavering durability, and inherent value. The unseen edge becomes the undeniable mark of quality.
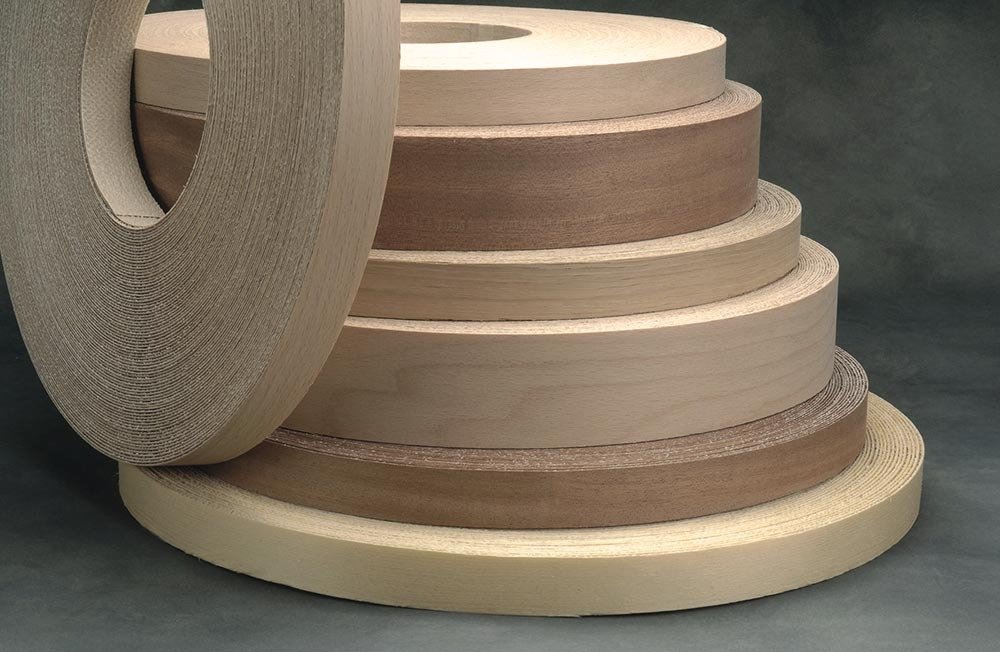
Ready to Elevate Your edge banding for kitchen cabinets?
Discover how our cutting-edge solutions, rigorous quality, and dedicated partnership can protect your reputation and define the next generation of kitchen excellence. Contact our technical team today for samples, specifications, and a consultation tailored to your production needs. Let’s build cabinets that truly last.
Leave a Reply