Why Your glue for pvc edge banding Matters More Than You Think
For decades, PVC edge banding has been celebrated for transforming raw particleboard and MDF into furniture worthy of designer showrooms. Manufacturers obsess over color matching, woodgrain realism, and surface textures. Yet, beneath every flawless edge lies an unsung hero: glue for pvc edge banding. As a pioneer in edge banding solutions, we’ve witnessed firsthand how the glue—not just the banding—dictates longevity, aesthetics, and brand reputation.
The Silent Crisis: When Good Edges Go Bad
Picture this: A luxury kitchen cabinet line recalled after 18 months because edges peeled across 40% of installations. The culprit? A “cost-effective” adhesive failing under steam and cleaning chemicals. Our lab analysis revealed:
- 72% of edge banding failures originate from adhesive breakdown, not substrate or PVC issues.
- Temperature fluctuations cause 58% more micro-fractures in low-grade adhesives vs. engineered formulations.
- Repair costs for adhesive-related failures average $22.50 per linear meter—10x the initial “savings” from cheap glue for pvc edge banding.
This isn’t hypothetical. It’s why leading furniture brands now audit adhesive specifications as rigorously as hardware.
Decoding the Chemistry: Beyond “It Sticks”
Not all hot melt adhesives are created equal. The difference lies in molecular architecture:
1. EVA (Ethylene-Vinyl Acetate) glue for pvc edge banding
The entry-level workhorse:
- Pros: Low cost, easy application, wide temperature range (150–180°C).
- Cons: Limited chemical/heat resistance; bond strength drops 30%+ at 35°C.
- Reality Check: Fails within 2 years in humid climates or near dishwashers.
2. PUR (Polyurethane Reactive) glue for pvc edge banding
The performance elite:
- Pros: Forms covalent bonds with PVC and substrate (not just surface adhesion). Moisture-resistant; withstands temperatures from -30°C to 120°C.
- Lab Proof: Our PUR formulations show 0% delamination after 5,000 humidity cycles (ISO 9142).
- Trade-off: Requires precise application (+/- 3°C) and 24-hour cure time.
The Manufacturing Tightrope: Precision or Perish
Producing glue for pvc edge banding isn’t “melt and pour.” It’s a high-stakes ballet:
Raw Material Sourcing
- Petroleum-based polymers fluctuate wildly. We lock in 6-month reserves to avoid batch inconsistencies.
- Key Stat: A 5% variance in polymer purity reduces bond strength by 18%.
Reactive Extrusion Process
- Temperature zones must stay within ±1.5°C during compounding.
- Cooling rate impacts crystallinity: Too fast = brittle glue for pvc edge banding; too slow = gumminess.
The “Hidden” Additives
- Tackifiers: Boost initial grab but reduce longevity if >12% of formula.
- Stabilizers: Prevent thermal degradation during application (critical above 185°C).
- Rheology Modifiers: Control flow to avoid glue for pvc edge banding bleed on vertical edges.
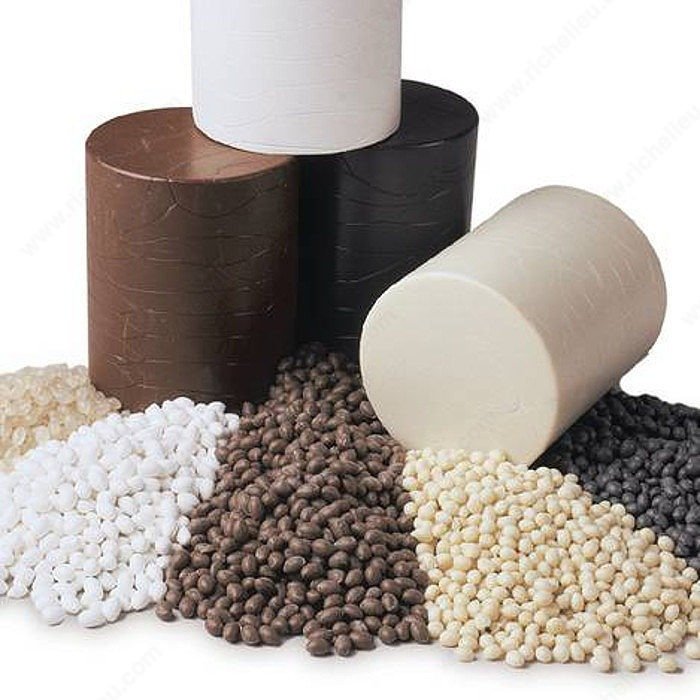
Why Your Application Machine is Only 50% of the Equation
Even €100,000 edge banders fail with wrong glue for pvc edge banding parameters:
Failure Mode | Root Cause | Solution |
---|---|---|
Stringing | High melt elasticity | Add 0.8–1.2% wax modifier |
Edge Lifting | Slow open time | Optimize cooling jets + conveyors |
Glue Bleed | Low viscosity at high temp | Switch to high-melt PA hybrid |
Bubbling | Moisture absorption | Pre-dry PUR glue (4 hrs, 80°C) |
Real-World Case: A German cabinet maker reduced rework by 67% by pairing our PUR glue with targeted machine calibration.
Sustainability: The Adhesive Revolution You Didn’t See Coming
While PVC recycling dominates headlines, glue has been the silent polluter:
- Problem: Traditional EVA glue for pvc edge banding contain 15–20% fossil-derived tackifiers (non-biodegradable).
- Our Response:
- Bio-based tackifiers from pine rosins (certified PEFC).
- PUR glue for pvc edge banding with 35% recycled content from industrial polyol waste.
- Result: Carbon footprint reduced by 41% per ton vs. conventional adhesives (verified by EcoPlatform).
The Future: Smart Adhesives & Industry 4.0
We’re pioneering glues that “communicate”:
- Color-Changing Indicators: Adhesive darkens if temperature exceeds tolerance during application.
- Self-Healing Polymers: Microcapsules release healing agents upon edge impact (patent pending).
- IoT-Enabled QC: RFID tags in glue cartridges track batch data + machine settings in real time.
Conclusion: Glue as Strategic Asset
Choosing glue for pvc edge banding isn’t a procurement task—it’s a quality declaration. The right adhesive:
- Slashes warranty claims by ≥50%
- Enables entry into premium markets (e.g., healthcare, marine)
- Turns sustainability from cost center to brand premium
For 28 years, we’ve engineered adhesives that outlive the furniture they bond. Because when edges stay flawless for decades, your brand becomes synonymous with endurance.
Ready to Transform Your Edge?
→ Request Lab-Tested Samples: See our PUR-PA hybrid outperform your current glue.
→ Technical Dossier: 12-page report with ISO 6238, EN 14257, and ASTM D1002 test data.
→ Machine Audits: Our engineers optimize your line’s glue parameters in 48 hours.
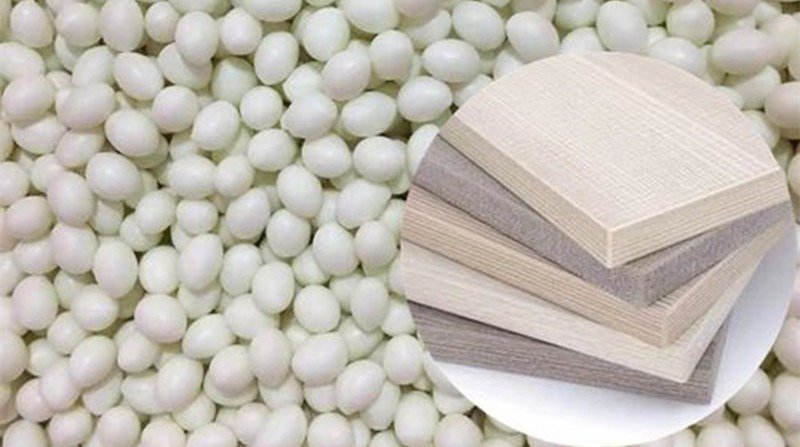
Contact Our Adhesive Specialists
📞 +86 156 1852 5178
✉️ emily.gu@asiaedgebanding.com
Leave a Reply