Hot Melt Glue
Edge banding hot melt glue is a specialized adhesive designed for edge banding of engineered boards, typically in solid form. It is specifically formulated to provide efficient and reliable edge banding solutions for the furniture manufacturing and woodworking industries.
- Solid State:
Edge banding hot melt glue is available in a solid form, making it easy to store and transport. Its stable physical state prevents any leakage or flow issues when not heated. - Heating and Melting:
During use, the hot melt glue is heated through specialized edge banding machines. Once the temperature reaches its melting point, the adhesive quickly transforms into a viscous liquid, making it easy to apply. - Coating and Pressing:
The melted hot melt glue is uniformly coated on the back of the edge banding strip. The edge banding machine then presses the edge banding strip tightly against the substrate. This process ensures an even distribution of the adhesive layer and a strong bond, enhancing the quality and durability of the edge banding.
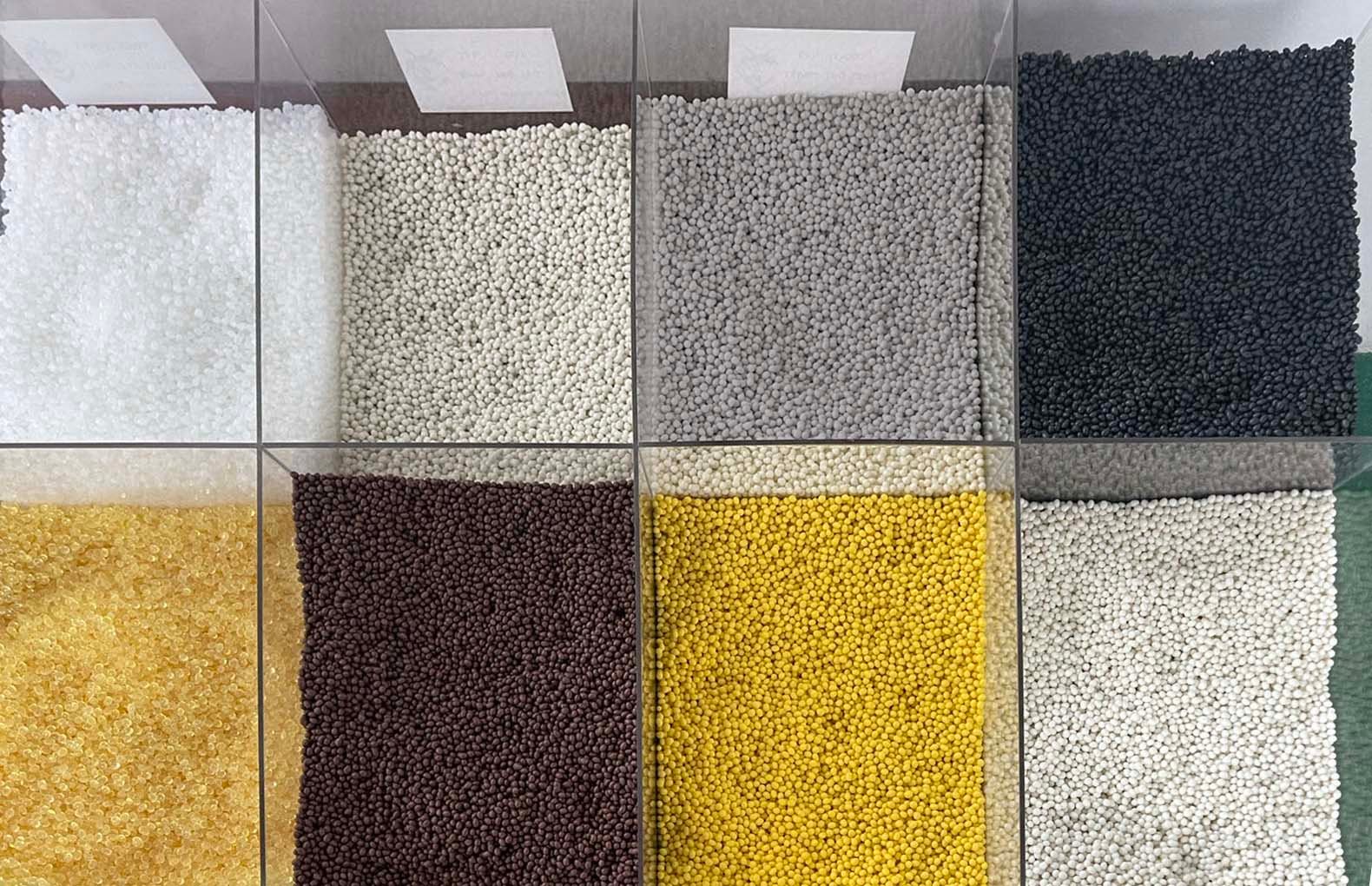
Classification of Hot Melt Glue by Application Temperature
A. High-Temperature Glue
- Application Temperature: 180–210℃
High-temperature glue is specifically designed for high-temperature environments and is suitable for applications that require resistance to elevated temperatures. This type of adhesive performs exceptionally well in industrial settings, often used in the manufacturing of automotive parts, electronic devices, and heavy-duty furniture. Due to its excellent heat resistance, high-temperature glue maintains strong adhesion even under high thermal conditions, preventing adhesive failure caused by heat.
B. Medium-Temperature Glue
- Application Temperature: 150–180℃
Medium-temperature glue is the most commonly used type of hot melt adhesive, widely applied in furniture manufacturing, cardboard packaging, and various everyday products. This adhesive provides good bonding strength and moderate heat resistance, making it suitable for a variety of material bonding needs. The application temperature range of medium-temperature glue makes it a flexible choice, capable of meeting the requirements of most industrial and household applications.
C. Low-Temperature Glue
- Application Temperature: 130–150℃
Low-temperature glue is specifically designed for applications requiring lower temperatures, particularly suited for heat-sensitive materials such as certain plastics, paper, and films. This type of adhesive can effectively bond at lower temperatures, reducing thermal damage to the substrates. The characteristics of low-temperature glue make it a popular choice in the packaging industry and for craft projects, ensuring that materials remain undamaged during the bonding process.
Softening Point and Application Temperature
Application Temperature:
The application temperature refers to the temperature of the adhesive on the glue roller of the edge banding machine. The glue can only achieve optimal bonding strength when the temperature on the glue roller reaches the specified application temperature. This temperature is crucial for ensuring that the adhesive fully utilizes its bonding capabilities during application. Proper control of the application temperature promotes even glue distribution and rapid curing, enhancing the quality and durability of the final product. By accurately managing the application temperature, manufacturers can significantly improve production efficiency, reduce material waste, and ensure consistent and reliable products.
Softening Point:
The softening point is an important indicator of the heat resistance of edge banding glue, representing the temperature at which the adhesive begins to soften upon heating. A higher softening point means that the adhesive is less likely to melt in high-temperature environments, thereby maintaining its bonding capacity. Generally, the softening point for edge banding glue ranges from 80 to 120℃, making it suitable for various applications and ensuring good adhesion performance even under elevated temperatures.
The Impact of Edge Banding Glue and Requirements for Hot Melt Adhesive
The Impact of Glue Lines on Furniture Appearance
The glue line between the edge banding material and the substrate directly affects the appearance of furniture. If the amount of adhesive applied is too large, the glue line will be prominent, negatively impacting the overall aesthetics. Conversely, if the adhesive is insufficient, it may weaken the edge banding’s strength, increasing the risk of peeling. Therefore, properly controlling the amount of adhesive applied is key to ensuring both the appearance and performance of the furniture.
Requirements for Hot Melt Adhesive for Substrates and Edge Banding Materials
- Control of Substrate Moisture Content
The moisture content of the edge banding substrate should be kept below 12%. Excessive moisture can lead to poor adhesion and an increased risk of adhesive failure. Therefore, before using hot melt glue, it is essential to ensure that the substrate is adequately dried. - Quality of PVC Edge Banding Adhesive
The adhesive on the back of PVC edge banding must meet quality standards; otherwise, it may result in weak bonding or even failure to adhere. Ensuring the adhesive’s bonding capability is a prerequisite for achieving a good edge banding effect. - Degreasing Treatment for Oily Substrates
For oily substrates, degreasing treatment is necessary. If the substrate is not degreased, the adhesive may not bond effectively, potentially leading to peeling. Therefore, it is crucial to ensure that the substrate surface is clean and free from grease before bonding.
Considerations for EVA Hot Melt Adhesive
EVA hot melt adhesive has poor solvent resistance, and it is especially important to be cautious when using solvents during the staining and spraying processes in industries that deal with wood pieces. If solvents penetrate excessively, diluents may seep into the adhesive layer, reducing the bonding strength of the hot melt glue and leading to peeling issues. Thus, during processing, efforts should be made to minimize contact between solvents and hot melt adhesive to ensure the reliability and durability of the edge banding.
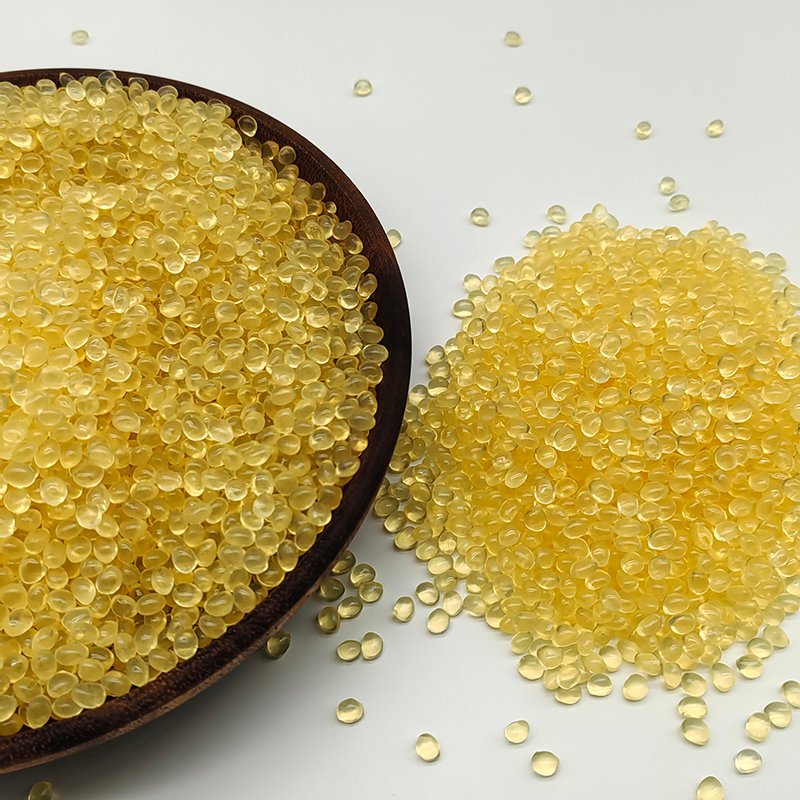
Yellow transparent
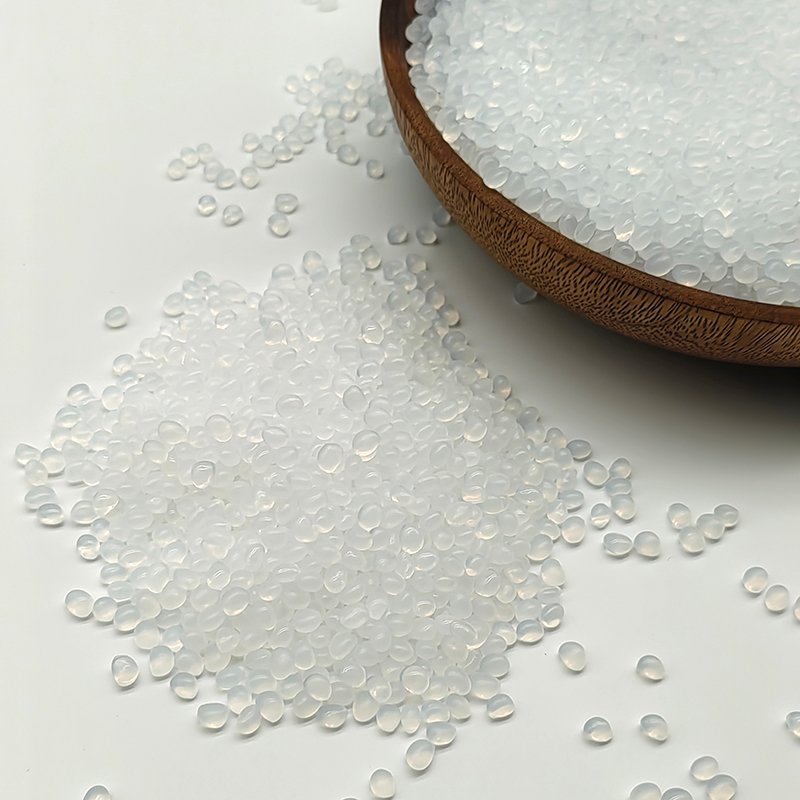
White transparent
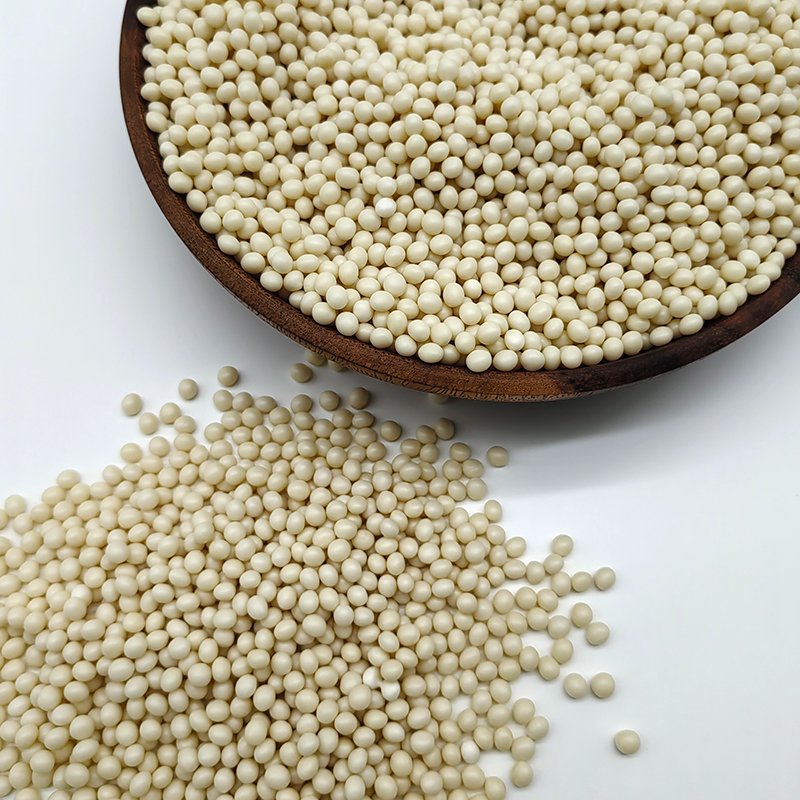
Apricot
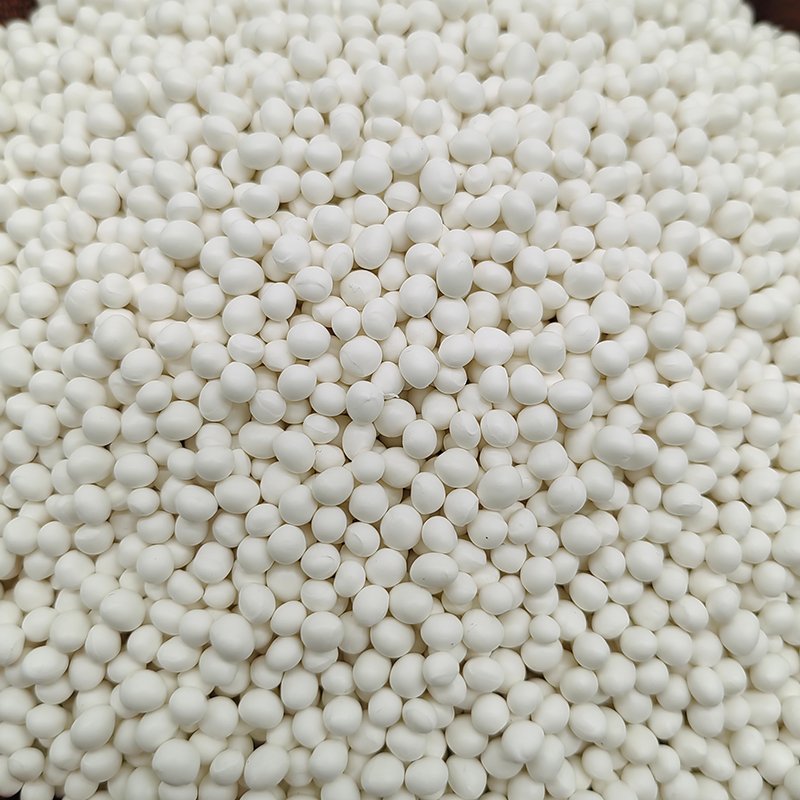
White
Precautions for Using Edge Banding Hot Melt Glue
When using edge banding glue, following certain precautions can ensure optimal performance of the adhesive and efficient operation of the edge banding machine. Here are some key considerations:
Adjust the Glue Pot Temperature
If the edge banding machine has not been in operation for more than 2 hours, the temperature of the glue pot should be lowered to around 100℃. This measure serves two main purposes:
- Prevent Carbonization: Prolonged exposure to high temperatures can lead to the carbonization of the glue, affecting its bonding performance and potentially damaging the equipment. Lowering the temperature effectively reduces this risk.
- Quick Reheating: When the machine is restarted, a lower temperature allows the glue to reach the required application temperature more quickly, thereby increasing production efficiency and reducing waiting time.
Regularly Clean the Glue Pot and Glue Roller
Regular cleaning of the glue pot and glue roller is crucial for ensuring proper equipment functioning:
- Remove Carbon Residue: Excess carbon buildup around the glue pot can compromise the heating system’s efficiency, leading to uneven heating and increased energy consumption.
- Clear Residual Adhesive: Residue on the glue roller can diminish the performance of the dispensing system, affecting the uniformity of glue application and, consequently, the quality of the final product. Therefore, regular inspection and cleaning of these components are essential.
Handling Residual Glue
If it is necessary to remove residual glue from the glue pot, proper procedures should be followed:
Use of a Scraper: Once the glue starts to melt, carefully use a scraper to remove it. Take care to avoid scratching the surfaces of the glue pot or glue roller during this process.
Heating Process: When in a cooled state, heat the glue pot to allow the glue around the edges to begin melting. This makes the residual glue softer and easier to remove.
Competitive Advantage
- Strong Adhesion
- Quick Setting Time
- Temperature Resistance:80-120°
- Versatility