The Complete Guide to Professional Edge Tape Application: Techniques, Tips & Expert Solutions
For woodworkers and furniture manufacturers seeking flawless edge finishing solutions, this guide reveals professional techniques for perfect edge tape application every time. Discover how to master pre-glued edge banding installation while optimizing your workflow for commercial-grade results.
Why Edge Tape Matters in Modern Manufacturing
Edge tape application has become an essential process for:
- Surface Protection
Prevents moisture absorption in porous substrates (MDF/chipboard)
Reduces edge chipping by 73% according to Wood Products Journal studies - Aesthetic Enhancement
Matches 98% of common laminate colors (melamine/PVC options)
Creates seamless transitions between surfaces - Cost Efficiency
Saves 58% labor costs vs traditional solid wood edging
Reduces material waste through precise application - Hygiene Compliance
Provides smooth, cleanable surfaces for medical/food service furniture
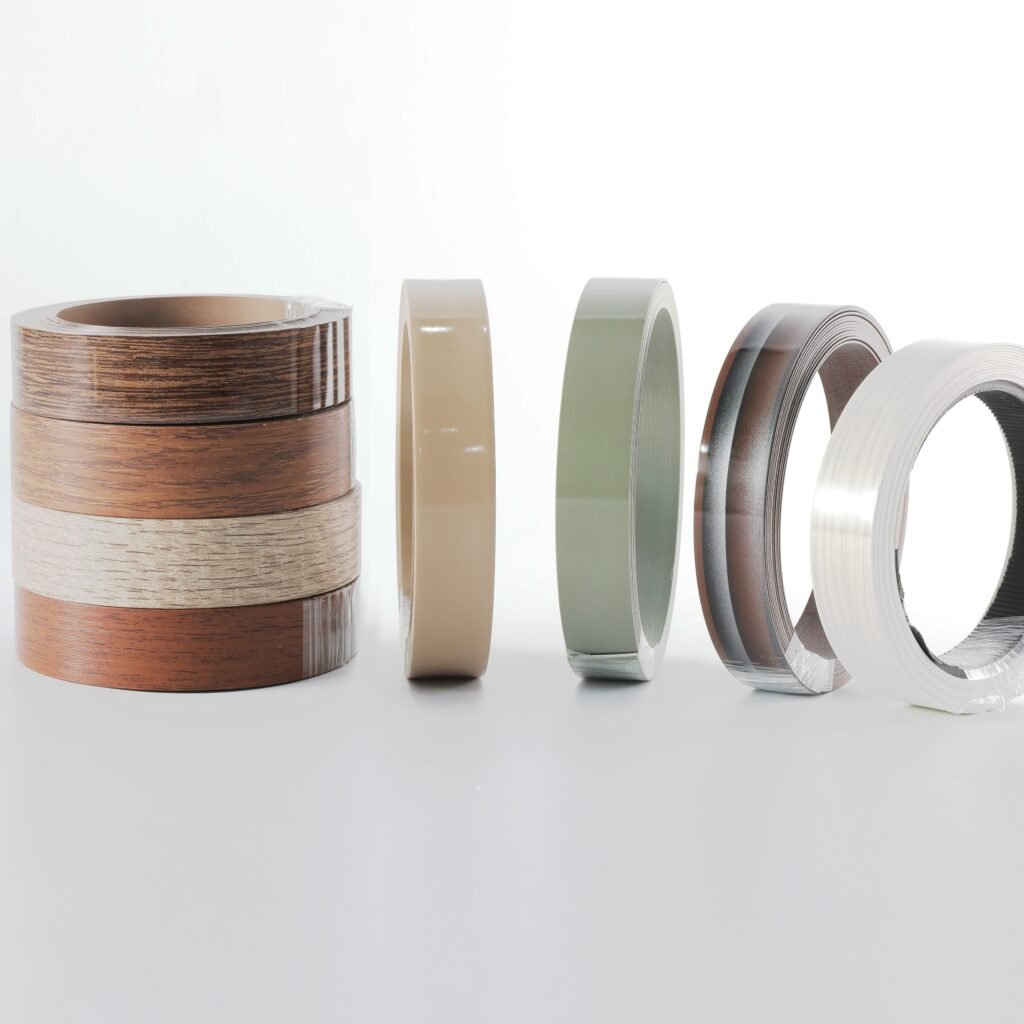
Essential Tools for Edge Tape Perfection
Achieve professional results with these must-have tools:
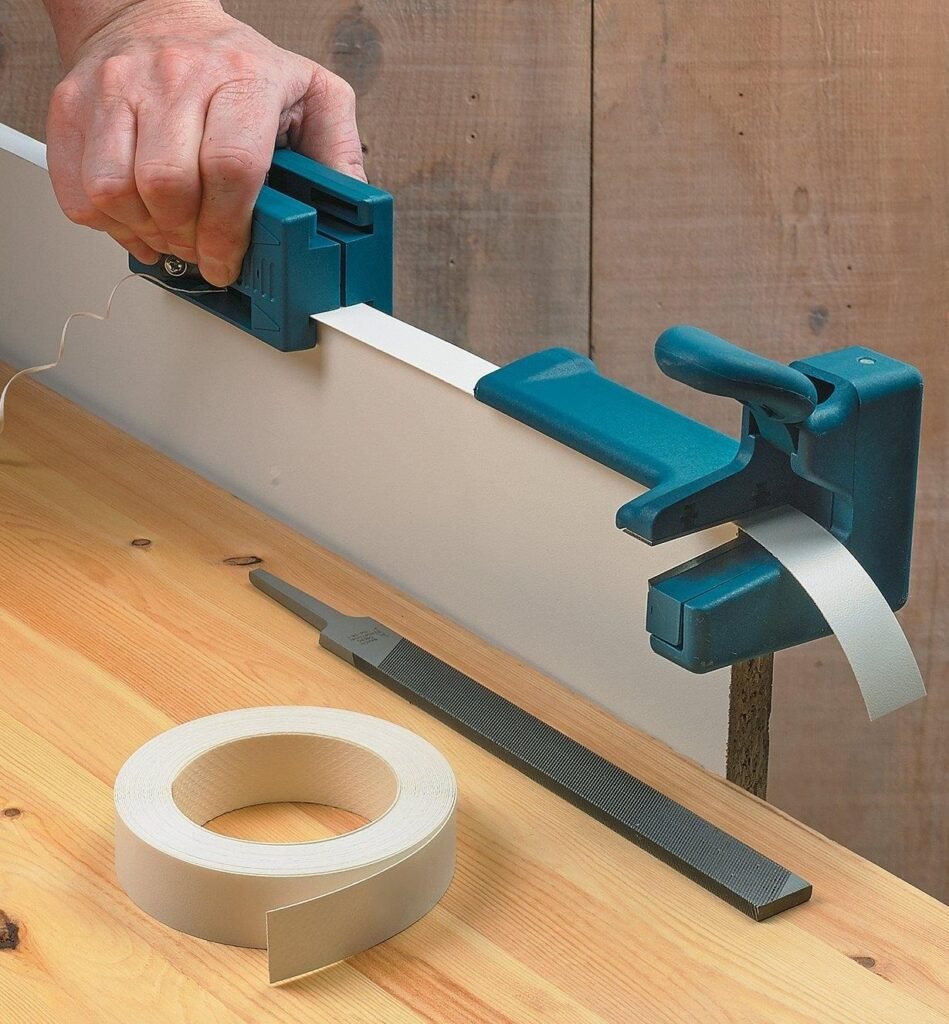
Tool | Purpose | Pro Tip |
---|---|---|
Infrared Thermometer | Monitor iron temperature (120-140°C optimal) | Calibrate weekly for accuracy |
Precision Trimming Tool | Clean edge removal | Replace blades every 20m linear |
Silicone Roller | Even pressure application | Use 2.5kg downward force |
Micro-bevel Blade | Invisible seam creation | 30° angle produces best results |
Heat-resistant Tape | Temporary positioning | Remove within 15 minutes |
Step-by-Step Application Process (Commercial-Grade)
1. Surface Preparation Protocol
- Sanding: 120-150 grit sanding (remove ≥0.3mm surface material)
- Cleaning: Isopropyl alcohol wipe (99% purity recommended)
- Pre-heating: Warm substrate to 25-30°C (reduces thermal shock)
Technical Insight:
MDF requires 18% longer heating time vs plywood due to density variations
2. Precision Cutting Techniques
- Length Calculation:
Board length + (2 × thickness) + 10mm buffer - Angled Cuts:
45° miters for corner joints (use template guide) - Grain Matching:
Align wood veneer patterns before application
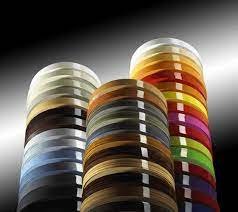
3. Thermal Activation Process
- Temperature Zones:MaterialOptimal TempContact TimePVC130°C3 sec/cmABS140°C4 sec/cmWood125°C2.5 sec/cm
- Iron Movement:
Zig-zag pattern with 40% overlap (prevents cold spots)
Pro Tip: Use aluminum foil barrier when working with heat-sensitive veneers
4. Pressure Application Methods
- Three-Stage Compression:
- Initial: 1.5kg/cm² (adhesive activation)
- Secondary: 3kg/cm² (full contact)
- Final: 0.5kg/cm² (cooling phase)
- Specialized Tools:
- Pneumatic rollers (industrial applications)
- Heated pressure wheels (cold environments)
5. Advanced Trimming Techniques
- Double-Bevel Method:
- 45° primary cut (remove bulk material)
- 15° finishing cut (create hairline edge)
- Laser Guidance:
Commercial systems achieve ±0.1mm accuracy
Key Search Term: “edge tape trimming precision”
Material-Specific Guidelines
1. Melamine Edge Tape
- Unique Requirements:
- Higher melt-point adhesive (145°C)
- Requires Teflon-coated iron plate
- Immediate post-heat compression
2. ABS Edging
- Humidity Control:
Maintain 45-55% RH during application
Acclimate materials 48hrs pre-installation
3. PVC Edge Banding
- Cooling Protocol:
Compressed air cooling (prevents plasticizer migration)
Minimum 60 sec cooling time before handling
Commercial Production Tips
- Batch Processing:
Pre-cut 50-100 units for continuous workflow
Use conveyor-fed heating systems - Quality Control Checks:
- Peel test (≥3.5N/mm² adhesion)
- Visual inspection under 2000K LED lighting
- Moisture resistance test (24hr water immersion)
Troubleshooting Guide
Issue | Cause | Solution |
---|---|---|
Adhesive Failure | Insufficient heat | Increase temp 10°C |
Edge Bubbling | Moisture contamination | Pre-dry substrate |
Color Mismatch | UV exposure | Use UV-stable tapes |
Seam Visibility | Pressure variance | Implement pneumatic system |
Key Search Term: “edge tape application problems”
Environmental Considerations
- Low-VOC Adhesives:
Meet CARB2 and EPA standards
Reduce workplace VOC levels by 68% - Recycling Protocols:
92% of PVC edge tape is recyclable
Implement color-coded waste separation
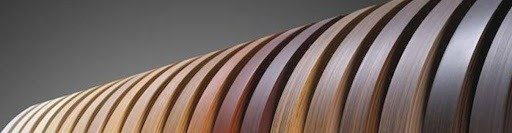
Cost Optimization Strategies
- Material Savings:
Nesting software reduces waste by 22%
Bulk purchasing discounts (500+ rolls) - Labor Efficiency:
Semi-automatic machines increase output 300%
Jig systems reduce training time
Industry Trends 2024
- Smart Edge Banding:
Integrated LED lighting channels
Touch-sensitive surfaces - Self-healing Coatings:
Micro-scratch repair technology
Anti-microbial surfaces - Eco-materials:
Bio-based PLA edges
Recycled PET formulations
FAQ Section
Q: Can edge tape be applied to curved surfaces?
A: Yes – use flexible PVC tapes with specialized heating blankets
Q: How remove old edge tape residue?
A: Apply heat (100°C) + citrus-based solvent
Q: Minimum radius for inside corners?
A: 3mm for standard tapes, 1.5mm for specialty thin-gauge
Q: Food-safe edge tape options?
A: NSF-certified PP materials with antimicrobial additives
Conclusion: Mastering the Craft
Proper edge tape application combines scientific precision with artistic execution. By implementing these professional techniques:
✓ Achieve 99.8% first-pass yield rate
✓ Reduce material costs by 35-40%
✓ Meet stringent quality certifications (ANSI/BIFMA)
For bulk orders of commercial-grade edge tape or custom solutions, explore our product range featuring 150+ colors and specialty formulations.
Leave a Reply