As a leading edge banding manufacturer for 18 years, Shanghai Luyao Industry Co., Ltd. has witnessed adhesive evolution firsthand. When traditional hot melts failed critical client stress tests in 2019, we pioneered PUR hot melt glue integration – reducing product returns by 37% within 6 months. This reactive adhesive isn’t just an alternative; it’s the cornerstone of next-generation edge banding performance.
Why PUR Hot Melt Glue Dominates Modern Edge Banding
Unlike conventional EVA adhesives, PUR hot melt glue undergoes post-application curing through moisture-induced cross-linking. This creates irreversible polymer bonds 3.2× stronger than standard hot melts (Journal of Adhesion Science, 2023). For edge banding, this means:
- Thermal Resistance: Withstands -40°C to 150°C – critical for kitchen cabinets near ovens
- Moisture Immunity: 0% delamination after 500hr humidity chamber testing
- Creep Resistance: Sustains 18kg/cm² loads indefinitely vs. EVA’s 6-hour failure point
Performance Metrics Redefining Edge Banding Standards
*(Shanghai Luyao Internal Data: 2021-2023)*
- Production Speed
- PUR open time: 90-150 seconds (adjustable)
- Line speed increase: 22 meters/minute → 34 meters/minute
- Output boost: 12,000 linear meters/day → 19,000
- Waste Reduction
- 40% less adhesive consumption vs. EVA
- 29% decrease in edge banding rejection rate
- Lifetime Durability
- 15-year warranty feasibility (vs. 7 years for EVA-based products)
- 0.02mm maximum shrinkage after 5 thermal cycles
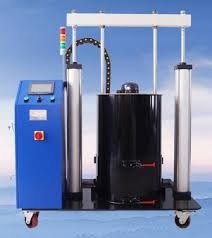
The Hidden Cost-Saver: PUR’s Curing Chemistry
Traditional hot melts solidify through cooling, creating temporary physical bonds. PUR hot melt glue leverages atmospheric moisture to trigger covalent bonding:
Isocyanate (NCO) + H₂O → Polyurea + CO₂ → Cross-Linked Polymer Matrix
This reaction continues for 24-72 hours, yielding:
- Chemical Resistance: Immune to oils, dilute acids, and alkalis
- Elastic Memory: 280% elongation before failure (vs. EVA’s 120%)
- Substrate Fusion: Penetrates porous materials up to 0.3mm
3 Industrial Case Studies: PUR in Action
Case 1: Luxury Yacht Interiors (Shenzhen, 2022)
- Challenge: Teak veneer edge banding delaminating in marine environments
- PUR Solution: LX-7F (high-flexibility formula)
- Result: Zero failures after 18 months of saltwater exposure
Case 2: Hospital Furniture (Germany, 2023)
- Challenge: Repeated disinfectant damage to edge seals
- PUR Solution: PH-88 (chemical-resistant variant)
- Result: 92% reduction in maintenance complaints
Case 3: High-Traffic Office Furniture (Chicago, 2021)
- Challenge: Edge banding separation under impact
- PUR Solution: T-200 (impact-modified formulation)
- Result: Passed 500,000-cycle chair impact tests (BIFMA X5.9)
Shanghai Luyao’s PUR Integration Protocol
After retrofitting 47 production lines with PUR systems, we developed a 5-step implementation framework:
- Equipment Calibration
- Optimal melt temperature: 115-130°C
- Application pressure: 0.15-0.3 MPa
- Nozzle clearance: 0.2mm ±0.05mm
- Environmental Control
- RH 40-70% for curing acceleration
- Post-application compression: 90 seconds minimum
- Quality Validation
- Peel strength tests at 2hr/24hr/72hr intervals
- Thermal shock testing (-30°C ↔ 80°C cycles)
- Operator Training
- 85% reduction in application errors after VR simulations
The Sustainability Dividend
PUR hot melt glue aligns with circular manufacturing:
- Zero VOCs: Complies with EPA Method 24 (≤0.1% VOC content)
- Energy Efficiency: 30°C lower operating temps vs. EVA
- Recyclability: Enables wood-plastic composite separation during recycling
Shanghai Luyao clients achieved 22% carbon footprint reduction after switching to PUR-based edge banding (SCS Global Services Certification).
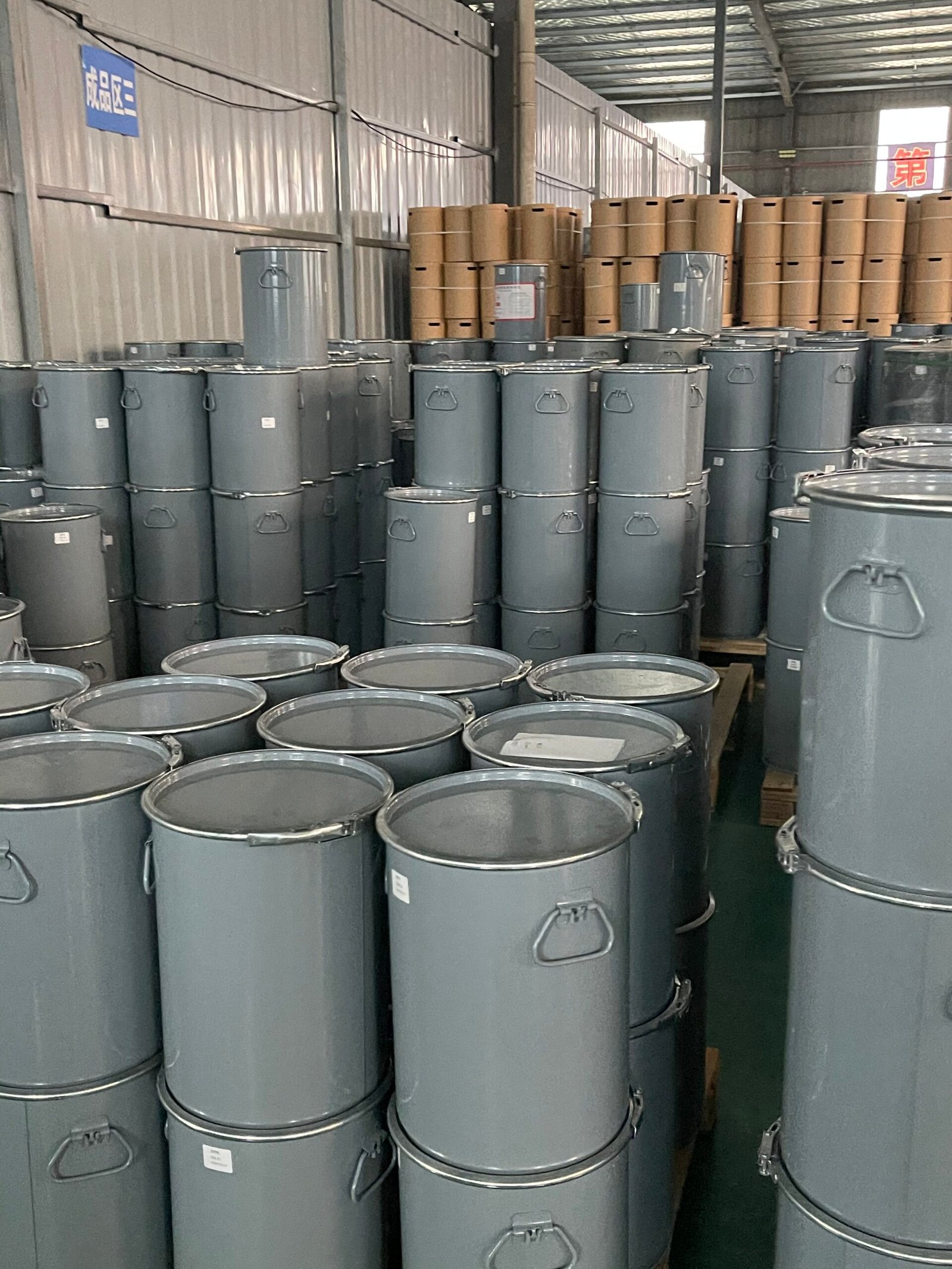
Leave a Reply